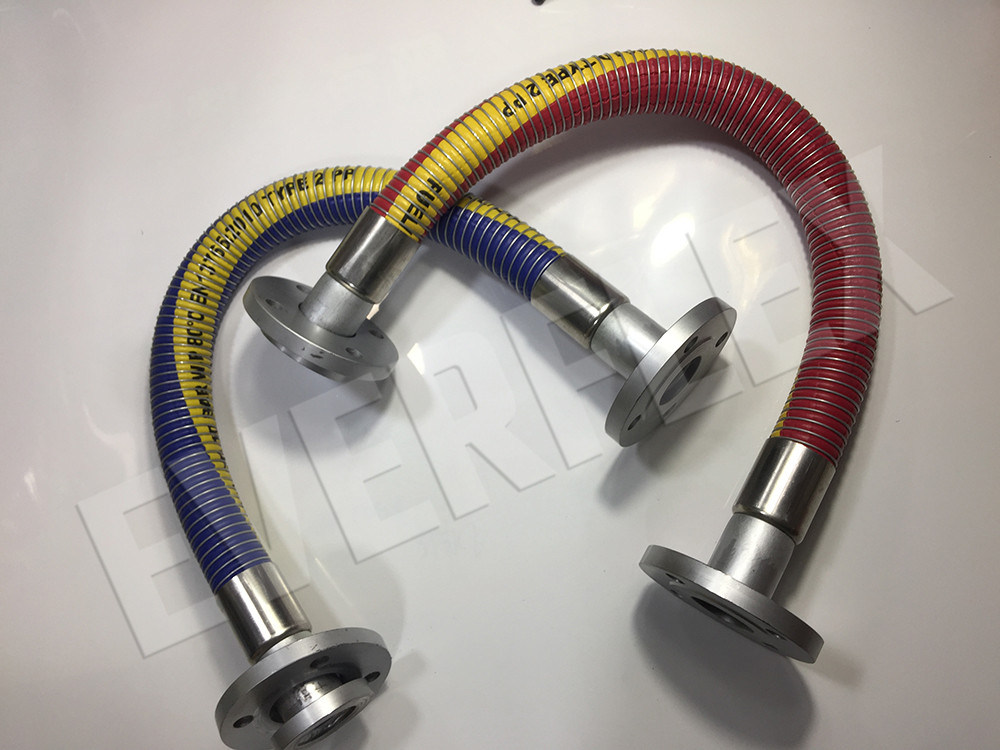
In the modern industry, we use hoses everywhere. While in the heavy industry, we mainly use rubber hose. Because it can deliver water, oil, chemical and many other mediums. However, in some special applications, the rubber hose will not be competent. For example, in the marine field, there will be problem to use a rubber hose. Because there is corrosion in the seawater and the salt mist. Thus after some time, those will corrode the rubber hose. Therefore, there comes the new material, composite hose.
However, many people said that there will be cracks on the surface of the composite pipe. In fact, a variety of factors can cause such problem. In general, improper operation during the production process will cause crack. Besides, the influence of the external environment will also cause cracks in the pipe. In addition, both of these will affect the use and lifespan of the pipe.
The specific reasons that cause cracks on flexible composite hose
First, in the rolling part of the finished product, the composite pipe has serious defects. Besides, serious scratch and serious wear of the roller groove can cause that.
Second, during rolling, there is impurity in the molten iron. The oxygen content is high and it forms oxides. If they are not cleaned during the process, cracks will occur.
Third, the molten iron contains a large amount of gas. When the molten iron solidifies, the gas is discharged and bubbles are formed. The bubbles close to the outer layer of the slab become subcutaneous bubbles. And they arranged vertically in a honeycomb pattern below the slab surface. Generally, the bubbles generated after billet rolling can be welded. But some subcutaneous bubbles are closer to the surface. When heating, while the surface of the steel billet burns, the bubbles will be oxidized. Then it will result in failure to weld and close. Therefore, cracks appears on the composite chemical hose.