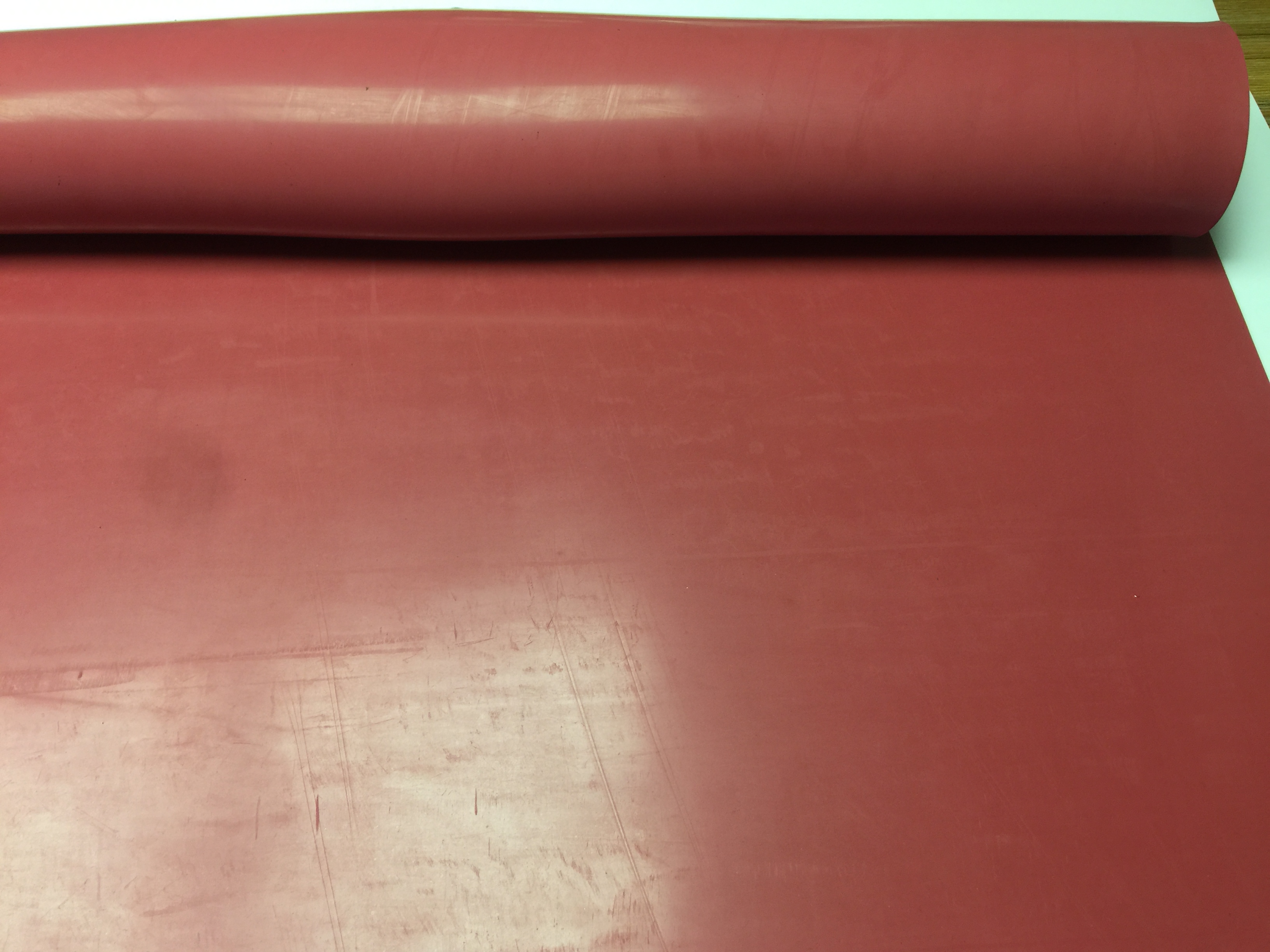
As we all know, rubber can be divided into three categories, natural rubber, synthetic rubber, and recycled rubber. These three rubbers are distinguished by their different chemical properties. Today, as a professional silicone manufacturer, we can distinguish between these different types of rubber.
Natural rubber, as its name suggests, refers to rubber made from natural rubber-producing plants. It comes from the high molecular weight hydrocarbons of the latex of many plants and is obtained by coagulation with chemicals, by drying, electrocoagulation and other methods.
Synthetic rubber is a common term and is a highly elastic polymer that is artificially synthesized. It is a necessary material for manufacturing aircraft, warships, automobiles, tractors, water irrigation and drainage machinery, medical equipment, etc. Synthetic high elastic polymers, also known as synthetic elastomers. The yield is only lower than synthetic resin (or plastic) and synthetic fiber. Its performance varies from monomer to monomer, and the performance of a few varieties is similar to that of natural rubber. The properties of synthetic rubber vary from monomer to monomer, and the performance of a few varieties is similar to that of natural rubber. Some synthetic rubbers have superior temperature, abrasion resistance, aging resistance, corrosion resistance or oil resistance to natural rubber. It has high elasticity under the conditions of use and has a certain modulus.
Recycled rubber is a rubber that has been treated with vulcanized corner scraps in the production of rubber products and has a certain degree of plasticity and can be reused. Referred to as reclaimed rubber. Recycled rubber is divided into outer tires, inner tubes, rubber shoes, etc. according to the different used rubber. Recycled rubber can partially replace raw rubber for rubber products, so as to save raw rubber and carbon black, which is also beneficial to improve processing properties and certain properties of rubber products. The regeneration process is a process in which the scrap rubber breaks part of the molecular chain and cross-linking point of the vulcanized rubber under the combined action of plasticizer (softener and activator), oxygen, heat and mechanical shear. Softeners act as expansion and plasticizers. Coal tar, pine tar, petroleum softeners, and cracked residual oils are commonly used. The activator can reduce the regeneration time and reduce the amount of softener. Commonly used activators are aromatic thiols and their zinc salts and aromatic disulfides. The reclaimed rubber production process includes comminution.
The above is the classification of different types of rubber by the professional rubber manufacturer everflex.